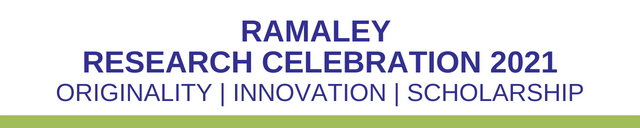
Presentation Title
Block Accelerated Fatigue Testing of Reinforced Thermoplastics
Loading...
Abstract
Fatigue is progressive damage resulting from repetitive fluctuations in material stresses and strains. It is the most common method of failure for engineering systems and is, therefore, the subject of extensive study in this field. The characterization of fatigue performance in materials is a vital part of product design, particularly in the automotive and aerospace industries where parts are subjected to demanding applications and high lifetime expectations. Traditional fatigue testing is expensive, time-consuming, and requires stable laboratory conditions – disturbances such as power outages or earthquakes can instantaneously invalidate data from a weeks long test. The concept of additive fatigue damage is well-known and states that the same percentage of cycling to failure generates the same amount of internal damage, regardless of the applied loading. This offers an interesting opportunity to significantly reduce the testing time required to characterize a material’s fatigue performance. This is done by consuming a high percentage of the material’s lifetime at high loading (low cycles) before transferring to a lower loading and extrapolating the data to calculate the total number of cycles to failure at this reduced load. In this study, the results of accelerated fatigue testing of reinforced thermoplastic composites are compared to a traditional fatigue background curve in order to evaluate the validity of fatigue testing methods engendered by cumulative damage theory.
College
College of Science & Engineering
Department
Composite Materials Engineering
Location
Winona, Minnesota
Presentation Type
Video (Prerecorded-MP4)
Block Accelerated Fatigue Testing of Reinforced Thermoplastics
Winona, Minnesota
Fatigue is progressive damage resulting from repetitive fluctuations in material stresses and strains. It is the most common method of failure for engineering systems and is, therefore, the subject of extensive study in this field. The characterization of fatigue performance in materials is a vital part of product design, particularly in the automotive and aerospace industries where parts are subjected to demanding applications and high lifetime expectations. Traditional fatigue testing is expensive, time-consuming, and requires stable laboratory conditions – disturbances such as power outages or earthquakes can instantaneously invalidate data from a weeks long test. The concept of additive fatigue damage is well-known and states that the same percentage of cycling to failure generates the same amount of internal damage, regardless of the applied loading. This offers an interesting opportunity to significantly reduce the testing time required to characterize a material’s fatigue performance. This is done by consuming a high percentage of the material’s lifetime at high loading (low cycles) before transferring to a lower loading and extrapolating the data to calculate the total number of cycles to failure at this reduced load. In this study, the results of accelerated fatigue testing of reinforced thermoplastic composites are compared to a traditional fatigue background curve in order to evaluate the validity of fatigue testing methods engendered by cumulative damage theory.