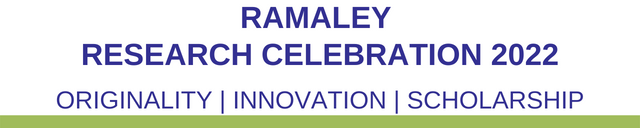
Presentation Title
Design of Experiments for drop tower impact and tensile welding of 3D printed structures
Abstract
Two studies were conducted during this EYRCM program project; Drop Tower Impact of 3D printed structures and welding studies of 3D printed structures. Most recommendations for fused deposition method (FDM) 3D printer settings revolve around the final aesthetic of the part and do not focus on the strength of the part created. FDM 3D printed parts are typically quite weak in the vertical direction and can be prone to significant damage from impacts. A design of experiments (DOE) was used to determine which settings used to print the part have the greatest effect on the final appearance and impact strength of the part. Flat panels were printed and a drop tower impact test was conducted on the specimens. JMP was then used to statistically analyze the effects of the DOE. Additionally, several methods were explored to weld together 3D printed parts. Tensile testing was conducted to compare the weld joints, and it was determined that strong, effective welds can be attained with simple methodology. These studies open doors for new 3D printed designs to be used as final parts and/or allows for the splicing of several 3D printed parts into larger structures like a jigsaw puzzle.
College
College of Science & Engineering
Department
Composite Materials Engineering
First Advisor
Eric O. Kerr-Anderson, Composite Materials Engineering Department
Location
Kryzsko Commons Ballroom
Start Date
4-20-2022 9:00 AM
End Date
4-20-2022 10:00 AM
Presentation Type
Poster Presentation
Session
1a=9am-10am
Poster Number
25
Included in
Design of Experiments for drop tower impact and tensile welding of 3D printed structures
Kryzsko Commons Ballroom
Two studies were conducted during this EYRCM program project; Drop Tower Impact of 3D printed structures and welding studies of 3D printed structures. Most recommendations for fused deposition method (FDM) 3D printer settings revolve around the final aesthetic of the part and do not focus on the strength of the part created. FDM 3D printed parts are typically quite weak in the vertical direction and can be prone to significant damage from impacts. A design of experiments (DOE) was used to determine which settings used to print the part have the greatest effect on the final appearance and impact strength of the part. Flat panels were printed and a drop tower impact test was conducted on the specimens. JMP was then used to statistically analyze the effects of the DOE. Additionally, several methods were explored to weld together 3D printed parts. Tensile testing was conducted to compare the weld joints, and it was determined that strong, effective welds can be attained with simple methodology. These studies open doors for new 3D printed designs to be used as final parts and/or allows for the splicing of several 3D printed parts into larger structures like a jigsaw puzzle.